Etoimos
Adventurist
Towards the end of 2021 it became apparent to me that while my current Jeep Gladiator was a really cool truck and it did great when off road, it had a few short comings that were just to big (or should I say to small??) to over look.
The first concern was that it was just to small. The interior was so tight I could almost touch the passenger door while driving. With the wife, kid and dog in the Gladiator, there was little room for anything else inside. That meant putting everything in the bed of the truck, and with the ACE Upper Decker, there was virtually no room in it either.
The interior of the new 2022 RAM Power Wagon is much more spacious with plenty of room for everyone. It also has more storage and creature comforts then the JT had as well. I’m loving the power rear window and auto up/down side windows (seriously, why are those not options on a $60k JT?) and my son Kiefer loves his new heated rear seat.
The other issues for me were the small fuel capacity and low fuel economy. I can deal with one or the other, but dealing with both when overlanding is a real pain. The PW actually gets a little less MPG, around 13mpg, then the JT did when daily driving and they both get about 10mpg when pulling the OGT Expedition 2.0 trailer. The advantage of the PW is the size of its fuel tank (31 gallons ) compared to the JT (22 gallons). An extra 90-ish or so miles can really make a difference when out in the middle of no where pulling the trailer.
The truck was built on Jan 18th 2022 and I flew down to picked it up on Feb 11th. The final MSRP price when delivered was $70k and some change. My price from Mark Dodge was $59,669.
After visiting with family down in Arkansas I made the 863 mile single day trip back to Colorado. It took 14 hours and 2.5 tanks of gas. I averaged 12.5mpgs on that trip running about 80mph for long stretches of it... up hill and against the wind.
Here it is in stock form at home in Colorado…
You will also notice in those photos and the ones below that I installed some Rok Blokz XL mud flaps as well. I ran these on my Jeep Gladiator and they held up very well to rock crawling. The main reason I have them is to help keep rocks from being thrown up onto the front of my OGT trailer. They should also help to preserve the powder coating on the sliders a little bit.
The first concern was that it was just to small. The interior was so tight I could almost touch the passenger door while driving. With the wife, kid and dog in the Gladiator, there was little room for anything else inside. That meant putting everything in the bed of the truck, and with the ACE Upper Decker, there was virtually no room in it either.
The interior of the new 2022 RAM Power Wagon is much more spacious with plenty of room for everyone. It also has more storage and creature comforts then the JT had as well. I’m loving the power rear window and auto up/down side windows (seriously, why are those not options on a $60k JT?) and my son Kiefer loves his new heated rear seat.
The other issues for me were the small fuel capacity and low fuel economy. I can deal with one or the other, but dealing with both when overlanding is a real pain. The PW actually gets a little less MPG, around 13mpg, then the JT did when daily driving and they both get about 10mpg when pulling the OGT Expedition 2.0 trailer. The advantage of the PW is the size of its fuel tank (31 gallons ) compared to the JT (22 gallons). An extra 90-ish or so miles can really make a difference when out in the middle of no where pulling the trailer.
Ordering a factory build
The Power Wagon is the first vehicle that I have had built to order from the factory. With the almost non-existent dealer inventory and lack of options on them due to the chip shortages, I thought it made more sense to order the truck with exactly what I wanted on it. It also did not hurt that I found an out of state dealer that sold it to me for just over $10k off of MSRP. Below is what I ordered on Veteran’s Day of 2021: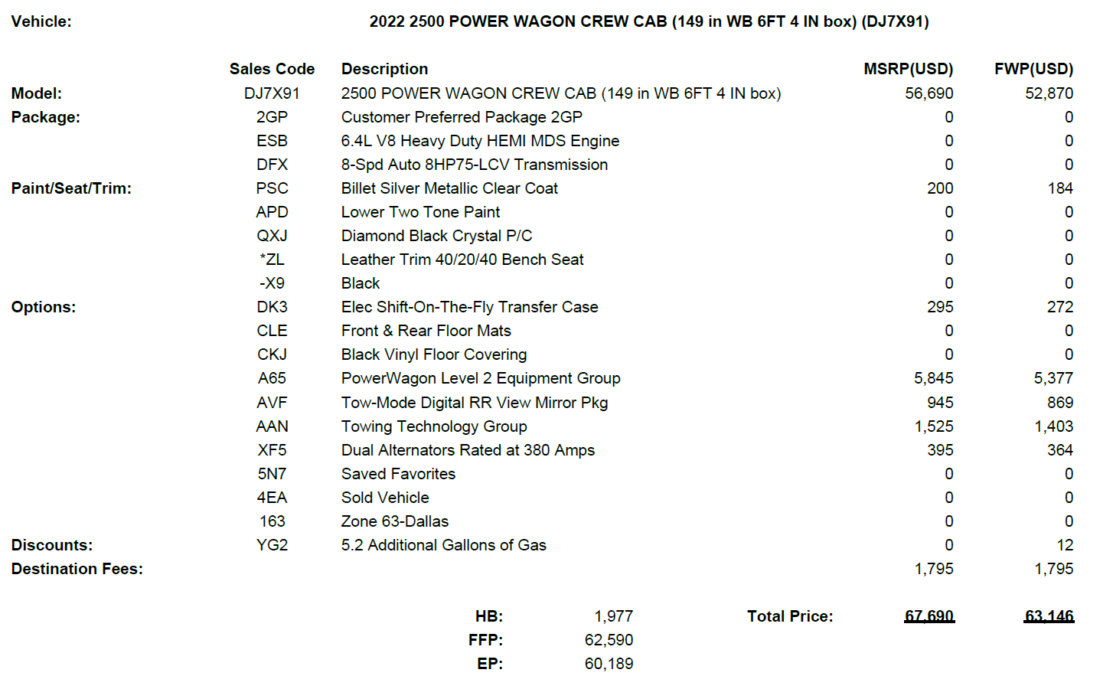
The truck was built on Jan 18th 2022 and I flew down to picked it up on Feb 11th. The final MSRP price when delivered was $70k and some change. My price from Mark Dodge was $59,669.
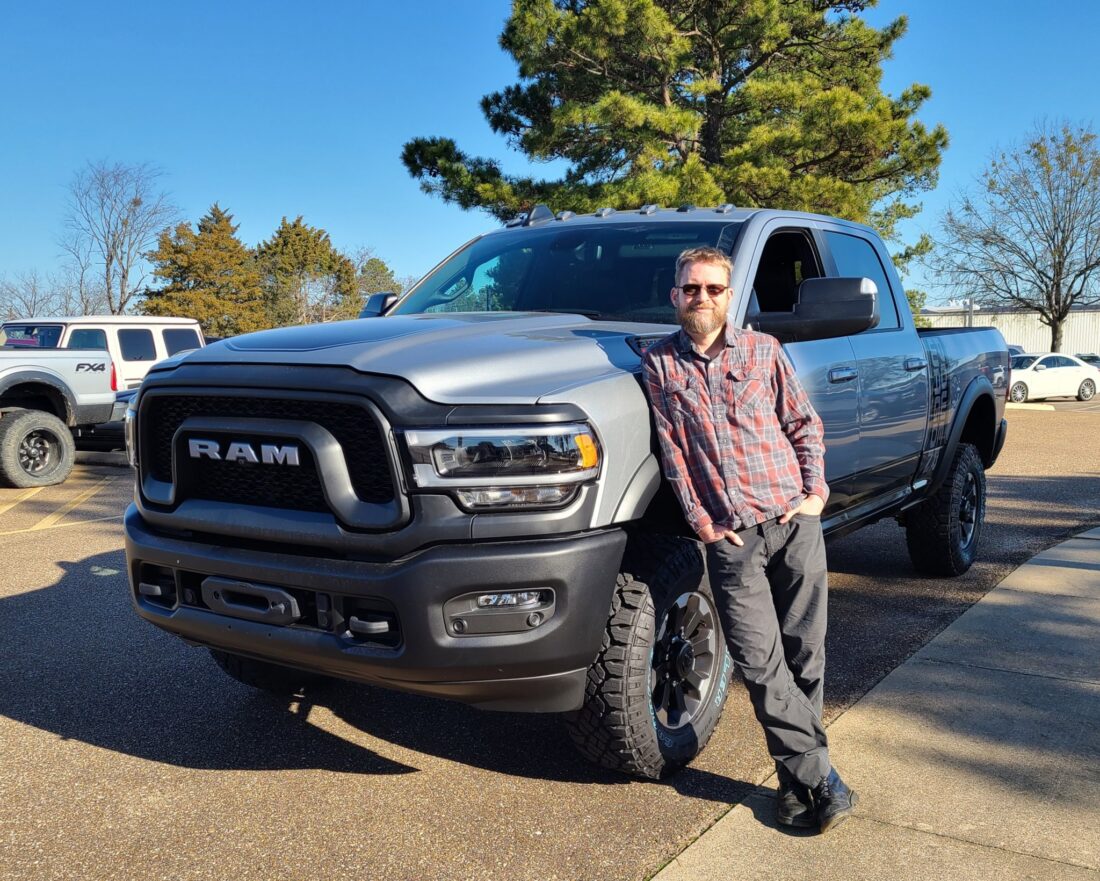
After visiting with family down in Arkansas I made the 863 mile single day trip back to Colorado. It took 14 hours and 2.5 tanks of gas. I averaged 12.5mpgs on that trip running about 80mph for long stretches of it... up hill and against the wind.
Here it is in stock form at home in Colorado…
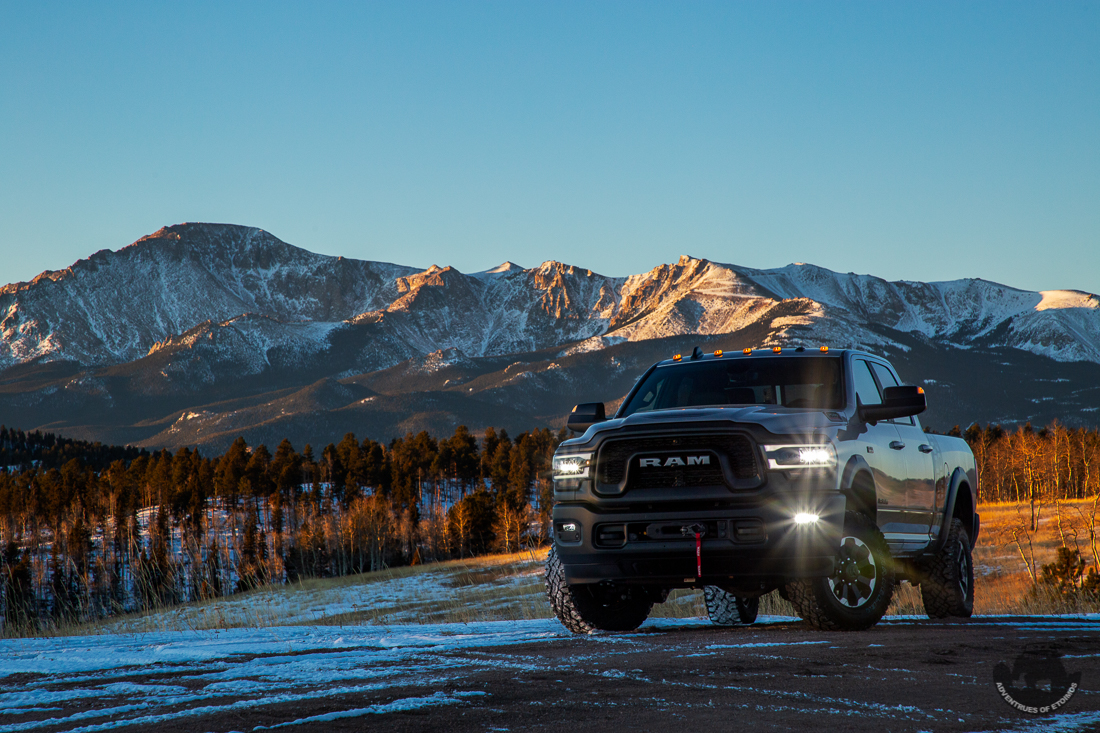
Let the modifications begin!
Rock Sliders and Mud Flaps
For those that don’t know, these trucks are heavy. 7280 pounds heavy in fact! Mine weighed 4340lbs on the front axle and 2940lbs on the rear axle in stock form. Add in all the mods and gear I’ll be carrying when out exploring and it was obvious that only some heavy duty rock sliders would do. Enter White Knuckle Off Road. White Knuckle offers their sliders in either .120 or .188 DOM tube thickness depending on your intended use of the the sliders. Since I would not purposely be doing any real rock crawling, I decided to go with the .120 DOM tubing to save a little weight while still giving me plenty of protection. I also opted for the full top plate and ordered the extra wide versions off of their secret menu.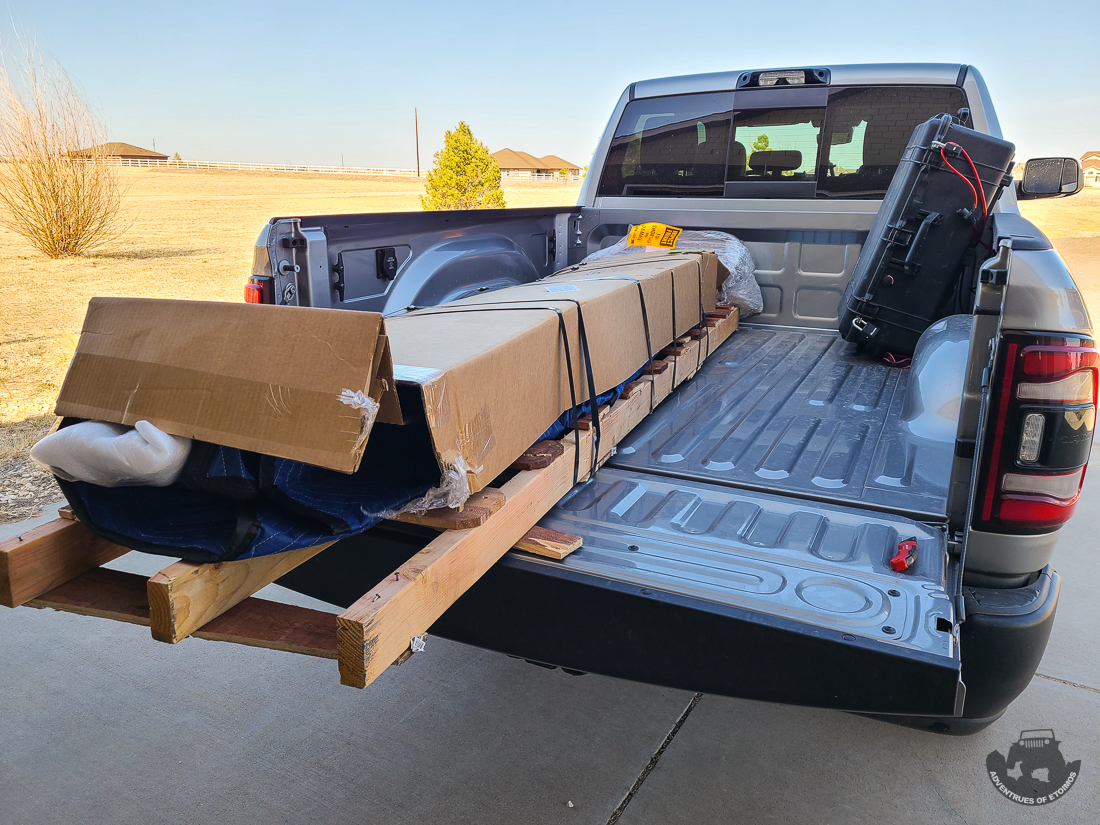
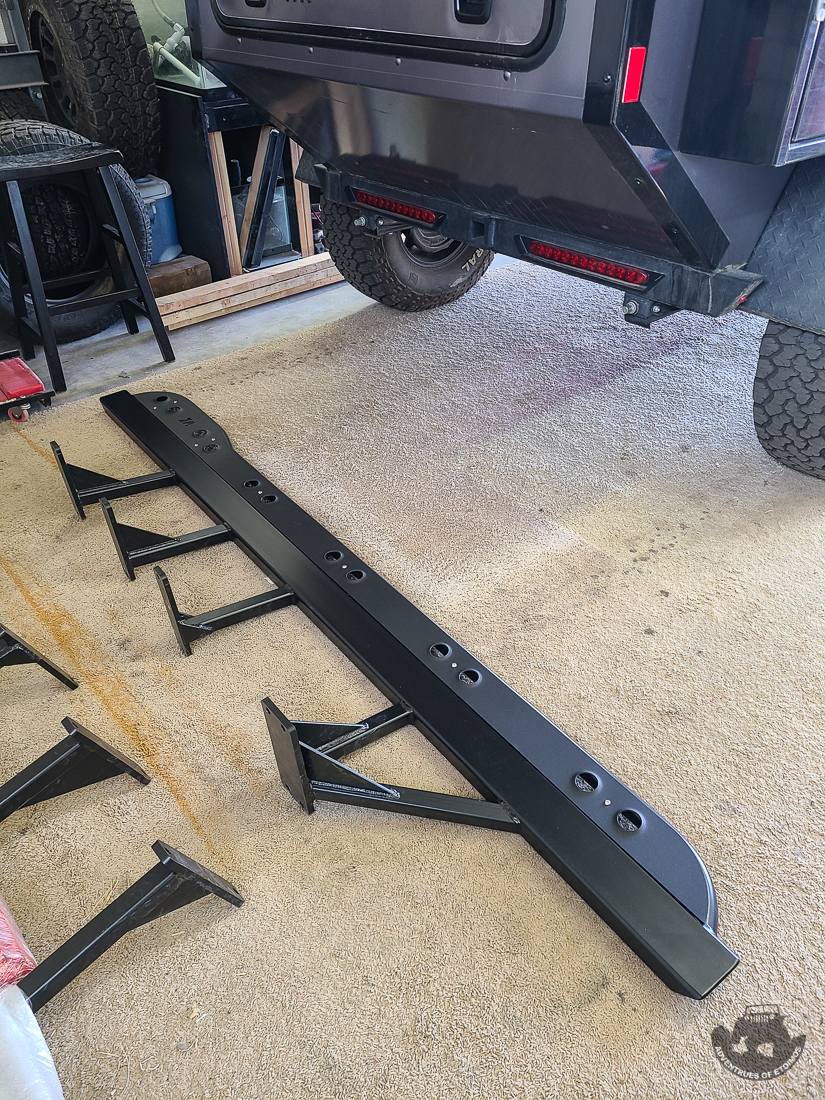
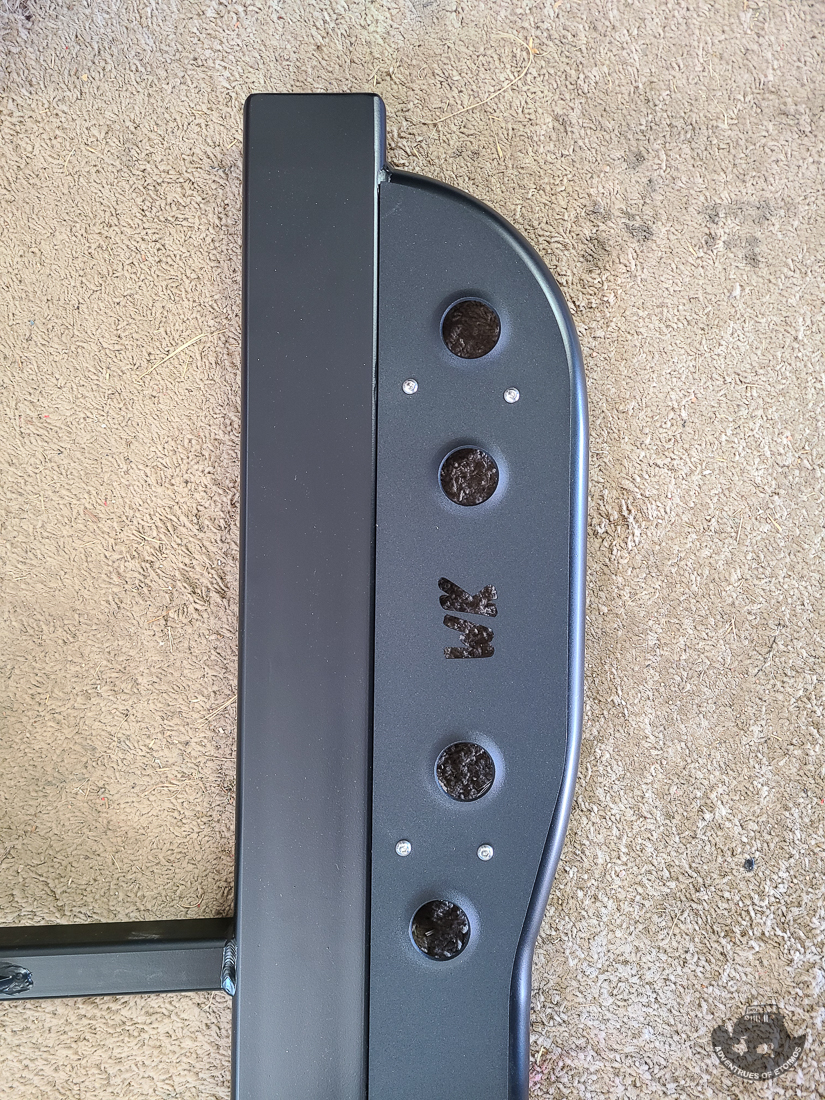
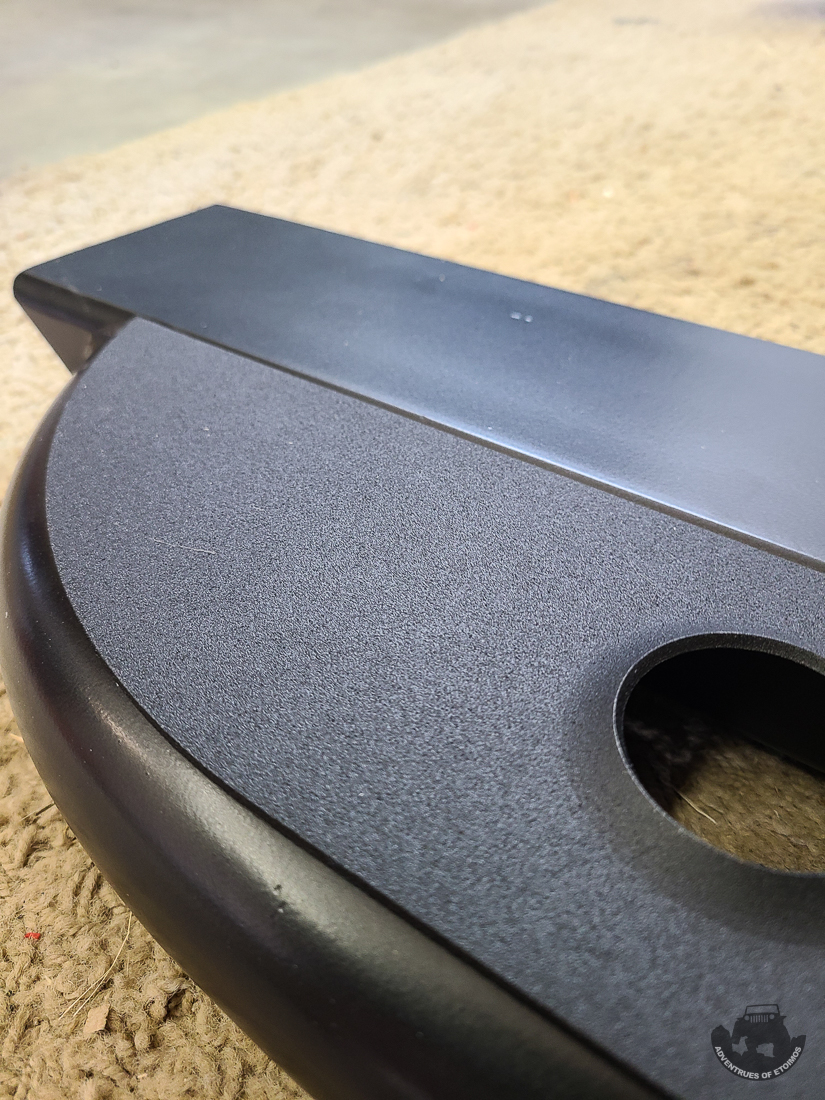
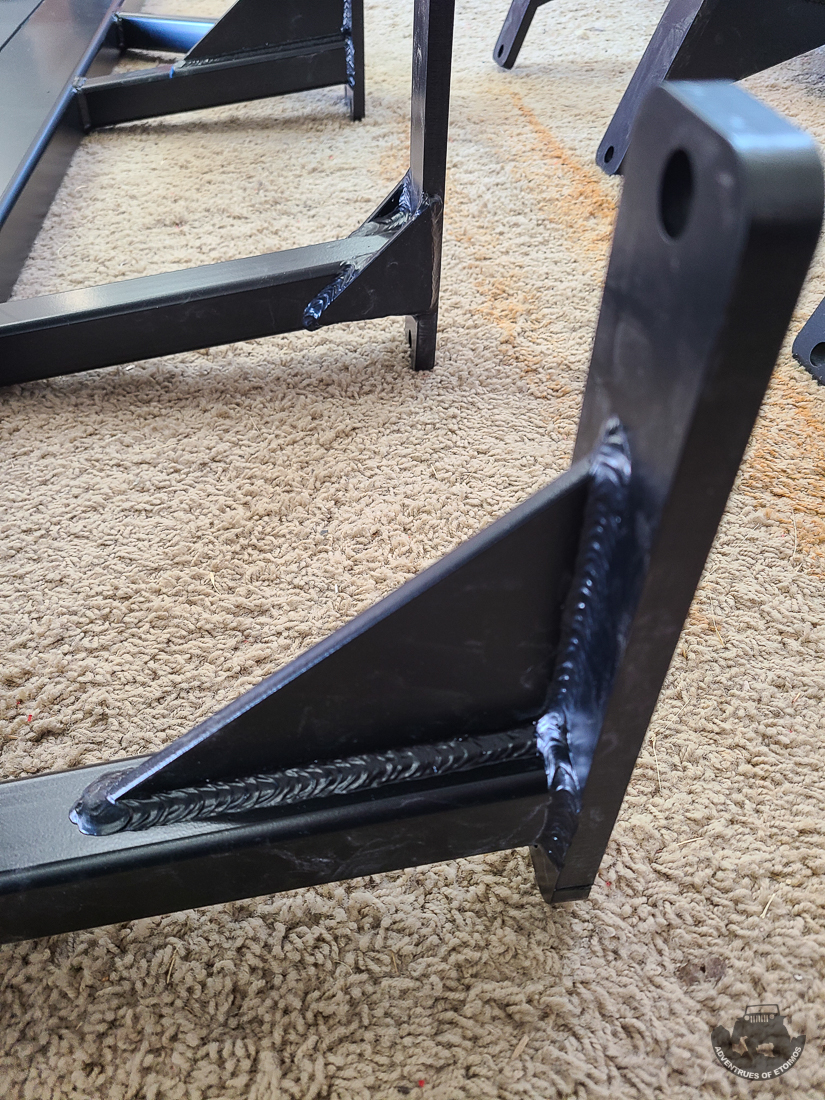
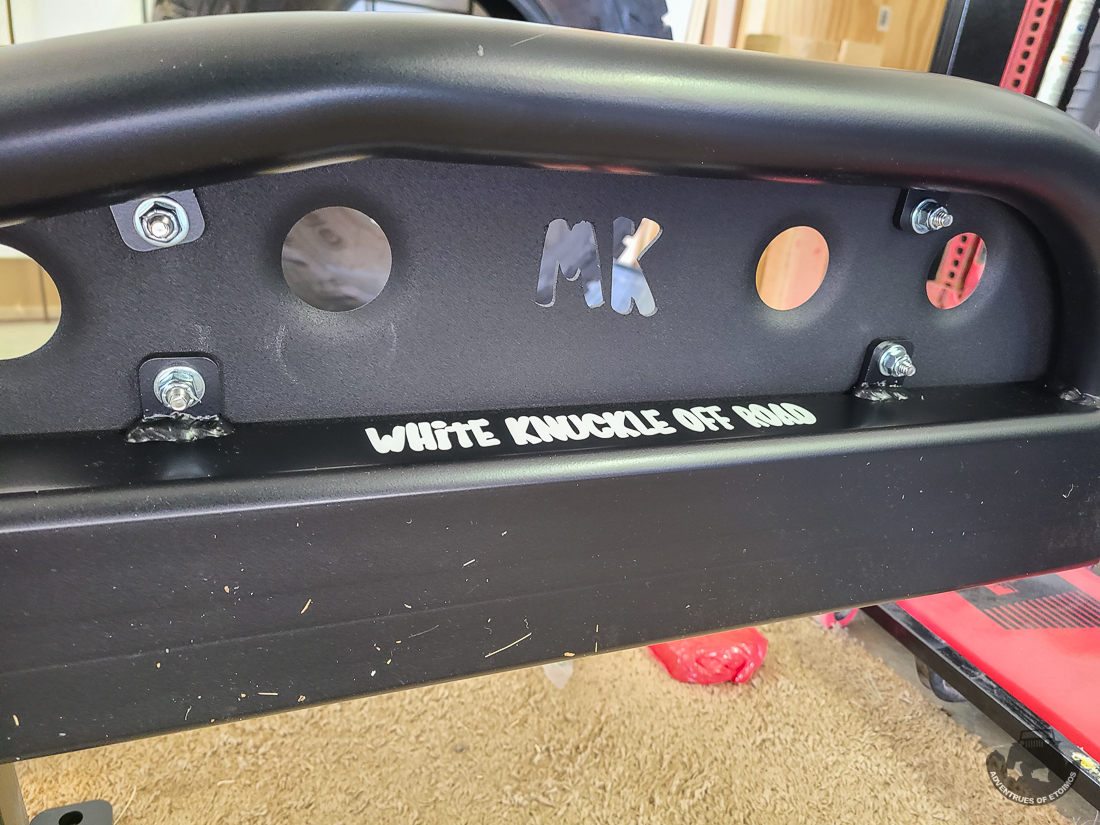
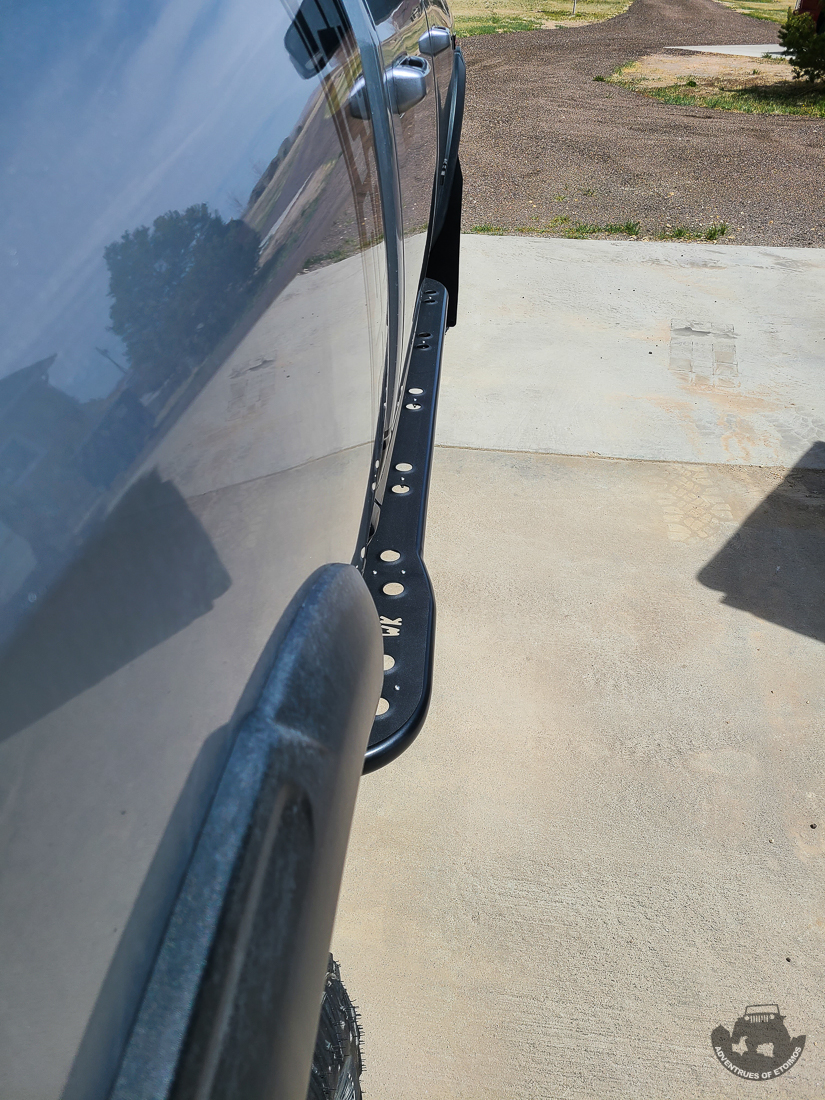
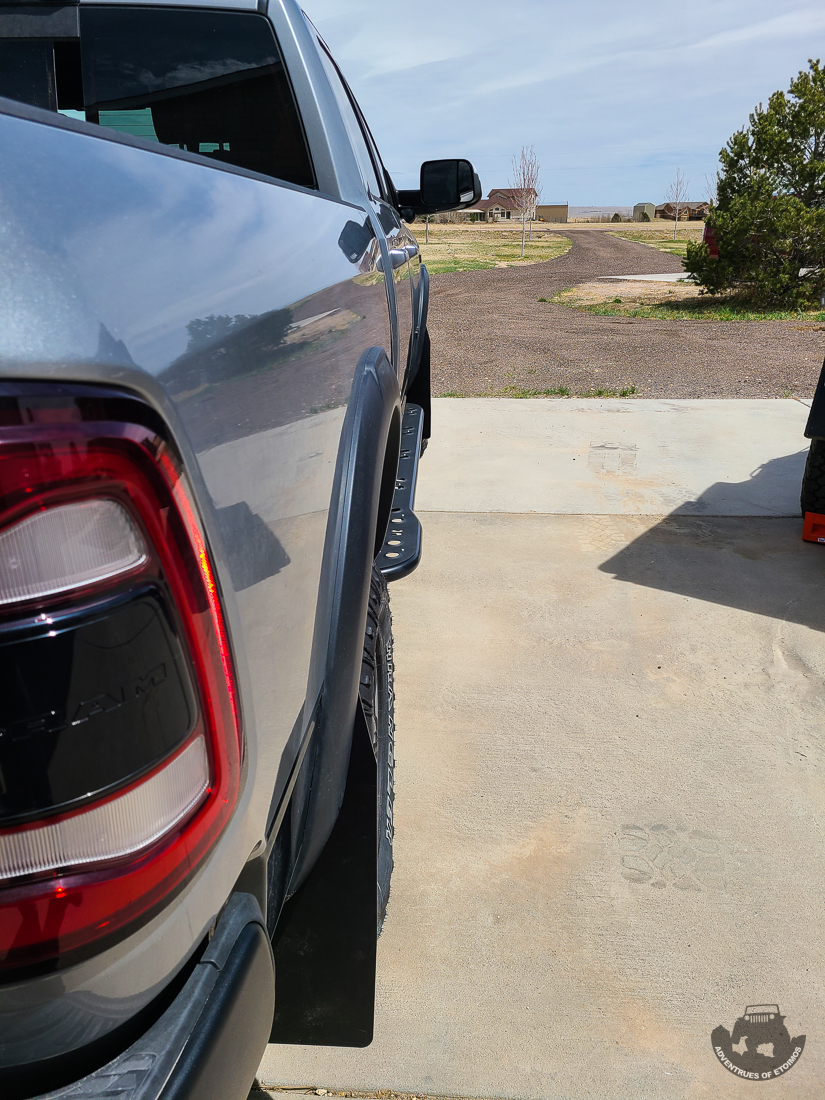
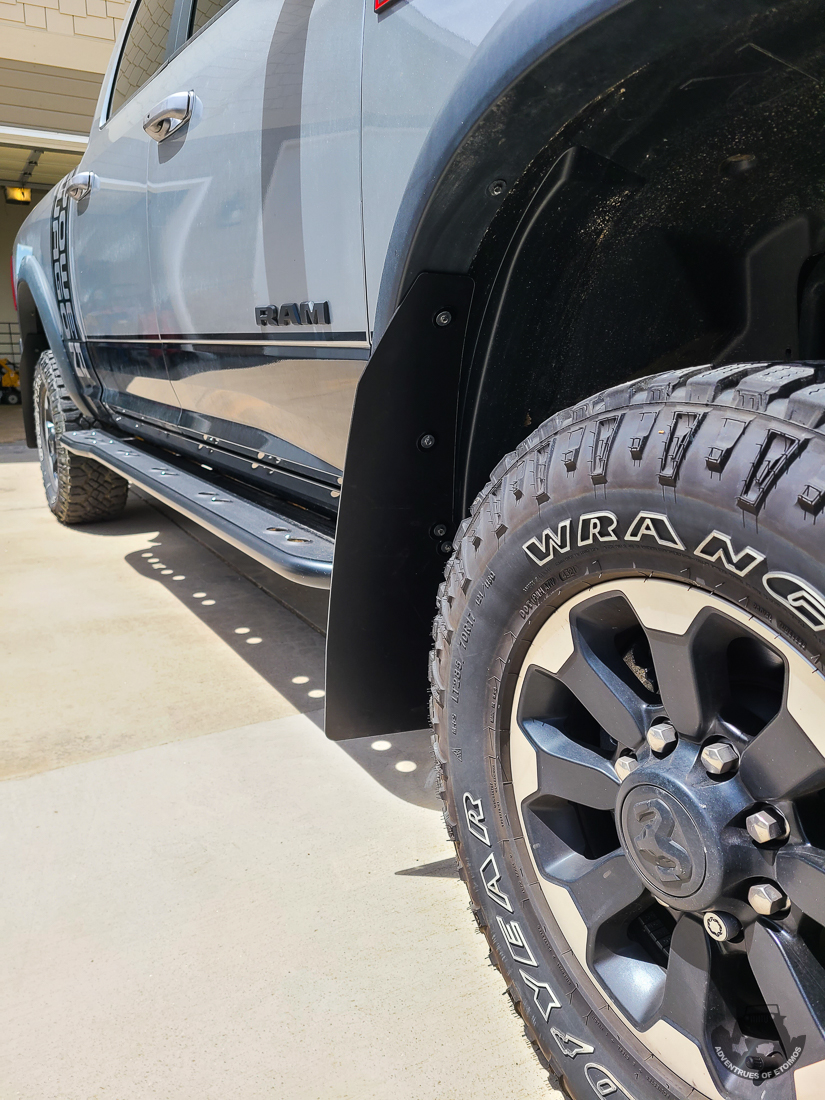
You will also notice in those photos and the ones below that I installed some Rok Blokz XL mud flaps as well. I ran these on my Jeep Gladiator and they held up very well to rock crawling. The main reason I have them is to help keep rocks from being thrown up onto the front of my OGT trailer. They should also help to preserve the powder coating on the sliders a little bit.

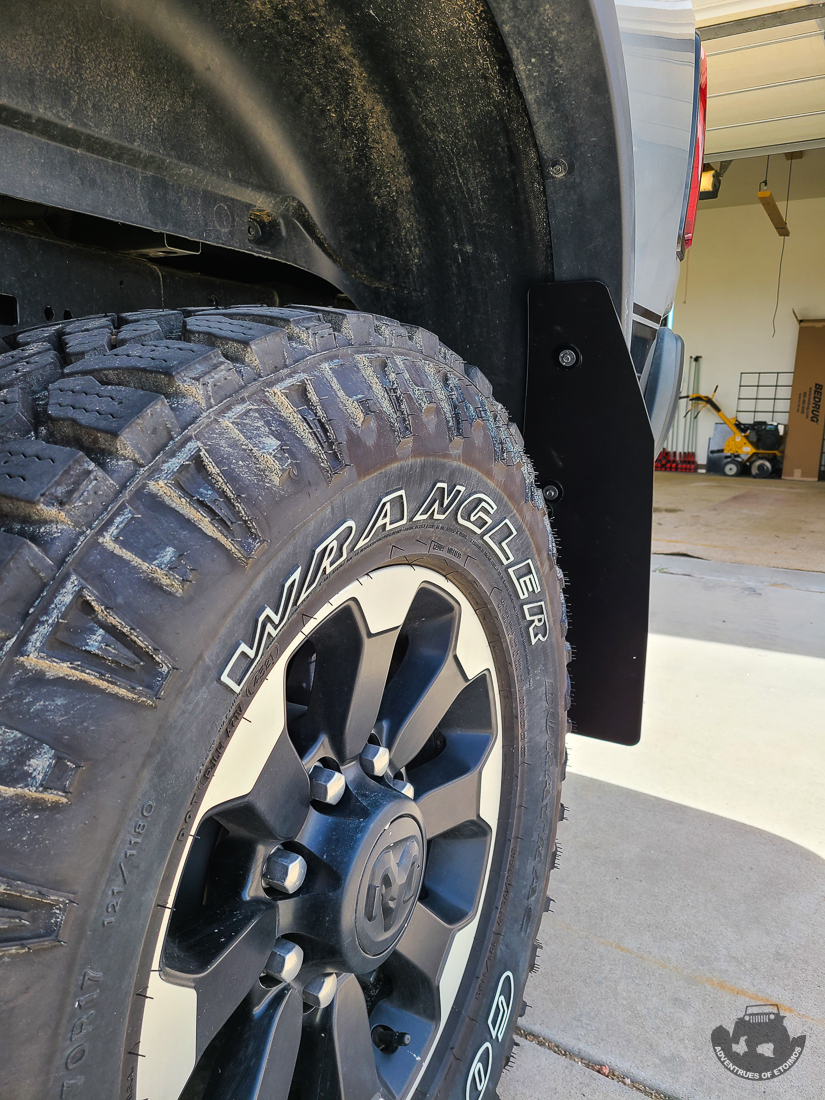
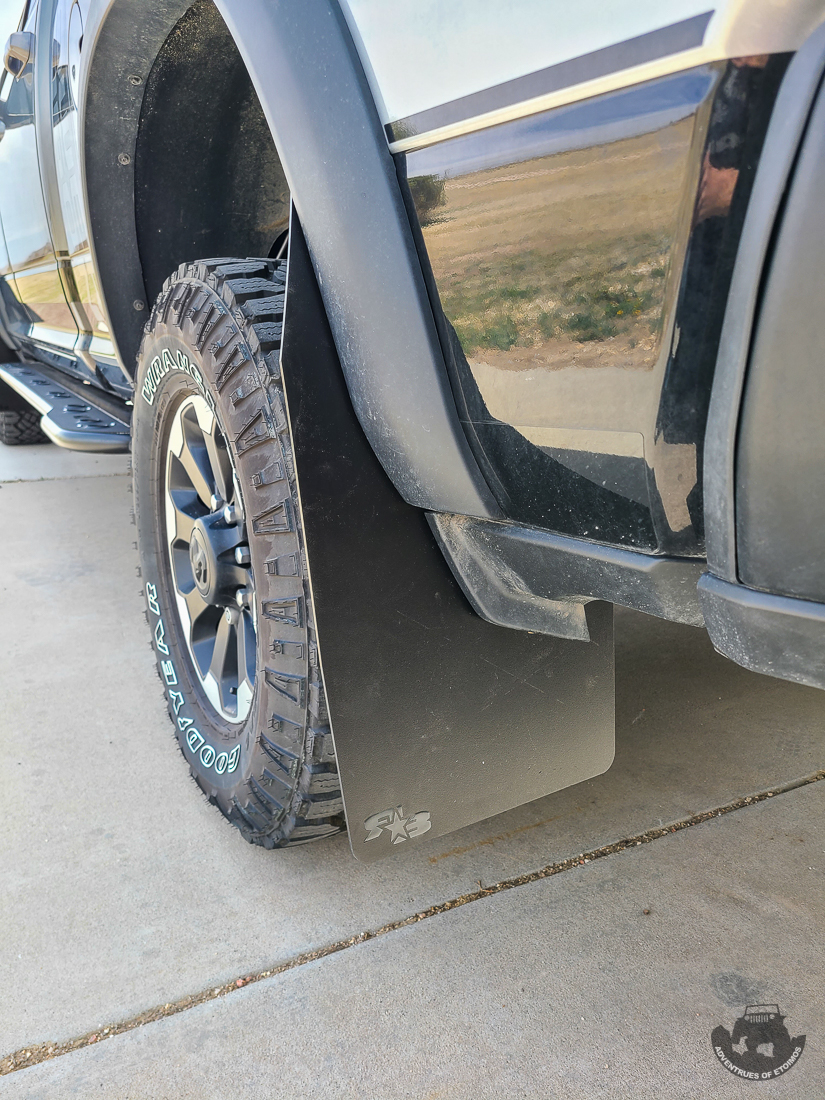